Hydraulic Seal
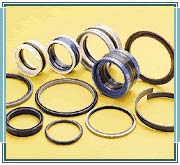
The seal is an agent that prevents leakage of oil from the hydraulic elements and protects the system from dust/dirt. A hydraulic seal is usually used to arrest both internal and external leakage of oil/gas/steam. It maintains pressure, prevent loss of fluid from the system and keeps out contamination in the system to enhance its service life and functional utility. In any kind of pressure actuated system, seal is necessary for rotary or reciprocating, static or dynamic system, steam, hydraulic or pneumatic medium.
Types of Seals
Seals may be categorized as per methods of sealing, areas of application, seal material, geometrical shapes of the seal used in the system etc.
Sealing may be
(a) Positive sealing that prevents even a minute amount of fluid from getting past (b) Non-positive sealing that may allow a small amount of internal leakage such as the clearance of a spool in its bore to provide a lubricating film.
Most commonly hydraulic seals are classified as:
(a) Static seals that are used when no relative movement occurs between the mating parts. The seal is usually compressed between two adjacent parts securing the two stationary parts together by fasteners.
(b) Dynamic seals are used between the surfaces of hydraulic parts where movement occurs and controls both leakage and lubrication. In certain dynamic seals wipers or covering boots are used to keep away dirt and other foreign materials. The motion encountered by dynamic seals may be either reciprocating or rotating or a combination of both.
Shapes
Owing to the various varieties of geometric shapes or configuration they take during fabrication, seals may be:
1. O-ring seal
2. Quad-ring seal
3. T -ring seal
4. V-ring seal
5. V-cup ring
6. Hat ring
Material
A seal can be categorized as per material. It may be made of:
* Leather
* Metal
* Polymers, elastomers & plastics
* Asbestos
* Nylon
Checklist for Hydraulic Seals
To ensure the desired function and long working life of a seal, there should be an appropriate installation process undertaken. The following factors need to be taken carea of:
1. The appropriate seal material with good compatibility should be selected for a specific application.
2. A favorable material for ease of fabrication should be selected for the hydraulic seal.
3. The seal contact surface should be fine finished and polished.
4. The clearance between the seal and the sealing surface should be kept small enough in order to prevent the seal from squeezing in between the clearance gap.
5. The cylinder piston rod seals should wipe out all undesired contaminants from entering the system as they are the main source of oil contamination.
6. During the mounting process, the seals should not be tilted due to the quality of the piston rod in order to prevent their premature failure.
7. For a longer service life of the seal, proper cleaning of the seal and sealing surface should be done frequently.
0 Comments:
Post a Comment
Subscribe to Post Comments [Atom]
<< Home